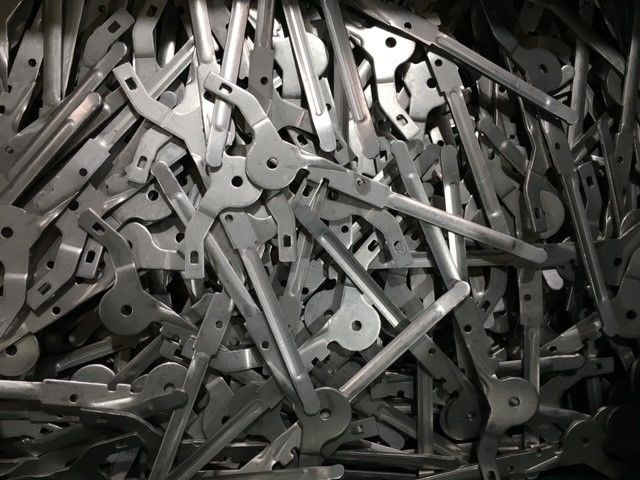
THERMIC INO 130: Health and safety as our priority
Acknowledged for its experience and its innovative solutions for customer safety and operations in heat treatment, MotulTech constantly strives to deliver the latest technology products to its customers. THERMIC INO 130, cold quenching oil based on GTL (Gas-to-Liquid) technology, has supported its customers to increase their safety to provide the safest working environment at extreme temperatures.
This innovative lubricant has higher flash point than standard mineral oils to lower the risks of fires when the oil is in direct contact with steel parts heated up to 900°C. THERMIC INO 130 helped industries who had fires and smokes at their plants to resolve these safety hazards providing safe and clean work environment.
GTL base oils have a lower volatility compared to standard mineral oil which gives a better comfort for its users. These oils do not contain heavy metals, chlorine, zinc and have minimal amounts of aromatics and sulfur. This innovative technology is designed to generate low mist and ensure a cleaner shopfloor working environment.
THERMIC INO 130: Smart efficiency
The low volatility of the GTL fluids leads to a significant reduction in oil consumption, with less top-ups. THERMIC INO 130 has also demonstrated an outstanding resistance to oxidation in comparison with standard quenching lubricants (Group I, Group II and Group III) which allows an extended bath life and stable performance. This economical gain is substantial.
The reduction in oil oxidation also helps reducing low soot generation and sludges which ensure bright quenching with clean components.
This innovative formulation has a higher viscosity index than standard oils. Therefore, they have a better thermal stability, provides better cooling properties and lowers the risks for film breakages. It enables a constant quality of the parts and lowers the working temperature of the bath to decrease the energy consumption.